Call Center Eliminates Cleaning Downtime
Call Center Eliminates Cleaning Downtime & Reduced Fouling in Heat Exchangers
Application: Cooling Tower Basin Cleaning in Call Center
Solids: Sand, Silt, Scale, and Other Contaminants
Liquid: Water in Open Loop System
Problem/Challenge: Eliminate Cleaning Downtime and Reduced Fouling in Heat Exchangers
Problem: Saving energy and reducing water waste is on the minds of every commercial building manager. The world’s largest financial institutions are at the top of the field in responding to these concerns. For many, sustainability is key. For one major bank’s call center located in Idaho, system downtime had become a huge problem.
This call center and data center* is just one of many for this international financial institution. This company also has a call center in Ohio that has recently been rated with an Energy Star Certification of 84%, making it a particularly eco-friendly installation. They also have 54 other Energy Star rated centers and a LEED Certified center in Frankfurt, Germany.
These online and live customer service departments are responsible for assisting over 15 million clients worldwide. These departments are also touted as some of the best in the field. With such high expectations, it’s understood that these call centers would require a measure of redundancy as well as the ability to operate without any downtime.
When the bank discovered a problem with the chemical-free water treatment system in their call center, they realized their need for filtration. Solids accumulation in the cooling tower basin was responsible for downtime and fouling of their heat exchangers.
“We were told that the ‘heavy solids’ were causing deposit fouling and needed to be removed,” said the facilities engineer, “Downtime is not an option and the data centers must operate at peak performance 24/7.”
Solution: The team installed a LAKOS TowerClean, TCI-0280-SRV/ABV system to control the build-up of contaminants in the cooling tower basins. Within 24 hours, significant and measurable solids were removed from the cooling towers basins.
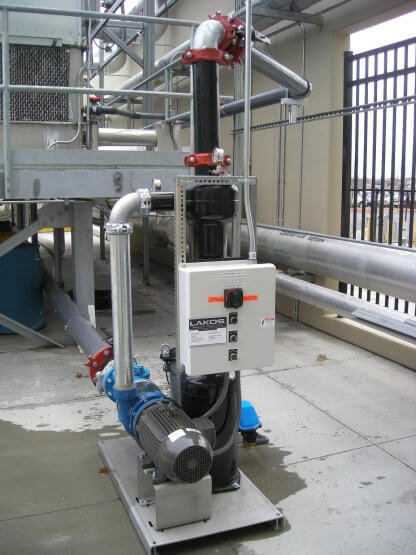
Citicorp Building, Meridian, ID – TCI-280 Clean Basin.JPG
Results: This new installation has allowed for peak performance of their condenser water equipment and has enabled the facility’s employees to focus their operational efforts on other components of the mission-critical facility.
It’s this innovative thinking and commitment to Best Practices that has convinced the bank to make LAKOS part of the solution for their facility.
The call center has now recently received an Energy Star Certification of 98%, thanks in part to their LAKOS filtration solution.
“The LAKOS Separator System using the HydroBooster nozzles is a great tool that is paying for itself in reduced cooling tower maintenance labor, water usage, and chemical treatment usage,” says the engineer who oversees the system. “I would recommend this product to everyone!
Why a Dual Purge System?
A Dual Purge System gives the facility manager the option to configure the purge of solids for either (a) a zero-maintenance ABV or (b) zero liquid loss SRV.
Automated Ball Valve (ABV) Purge – During heavy cooling demand times (such as Summer) the cooling tower system would incorporate the LAKOS zero maintenance approach. This allows the facility manager to allocate more time for other critical operations. This option allows solids to be purged directly into a sanitary drain for disposal.
Solids Recovery Vessel (SRV) – This option allows for a zero liquid loss approach to filtration. In less demanding cooler-weather seasons, the SRV can optimize water and chemical savings by collecting unwanted solids in a bag filter housing with minimum maintenance for removal.